Value Chain Meaning and Definition
A value Chain is a set of activities that a firm performs while operating in a specific industry to deliver a valuable product or service to the market. It is also defined as “A high-level model of how businesses receive raw materials as input, add value to the raw materials through various processes, and sell finished products to customers”. Porter’s Value Chain represents a system that explains how inputs are changed into outputs. In addition to the value chain definition, below video explains more aspects required to understand what is value chain?
Complexity of Value Chain Creation
Creating Value in Supply Chain?
Supply chain management is about creating net value. Early efforts at managing chains often focused only on cost reduction – on making the chain leaner. Unfortunately, these efforts sometimes reduced the ability to create value more than they reduced costs, for a net negative effect. As we will see, there is more to creating value through intelligent management than simply squeezing costs out of one or another activity in the chain.
Collaborative Value Chain in Supply Chain
There should be value-creating activities in the supply chain that transcend the activities of particular entities. Supply chains are generally organized by one strong firm called a channel master or nucleus firm—often a manufacturer, sometimes a powerful retailer, which often manages those activities. Nevertheless, the chain has to produce value for more than one stakeholder and generate value for the consumers or investors.
Complexities of Global Supply Chains
Management of global supply chains requires a balancing act among competing interests. Given the complicated nature of group dynamics, this can be a challenging task, especially in “worldwide” chains. Consider the rivalries that arise among and between the 50 American states, the 25 nations in the European Union, the various sects of any world religion, and the divergent cultures around the globe.
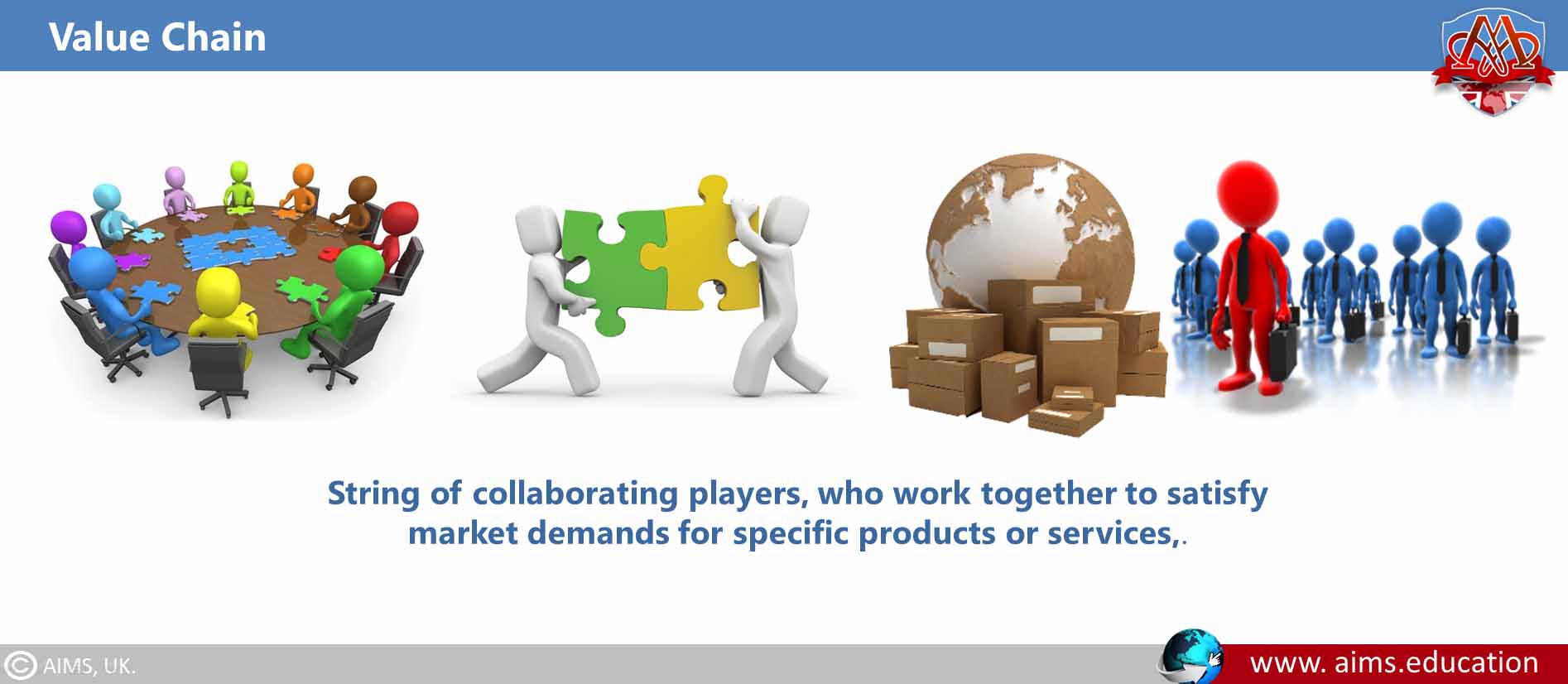
Supply Chain VS Value Chain
1. Key Components of Supply Chain Management
Supply chain management is defined as “the design, planning, execution, control, and monitoring of supply chain management systems to create net value, building a competitive infrastructure, leveraging worldwide logistics, synchronizing supply with demand, and measuring performance globally.” (Globally, in this case, it can mean either worldwide or applying to the chain as a whole rather than to a particular entity within the chain).
2. Understanding Value Chain in Supply Chain
The value chain definition of supply chain seems fairly solid when you consider the chain as linked organizations—supplier, producer, and customer connected by product, information, and payment flows. However, the supply chain is more accurately viewed as a set of linked processes that take place in extracting materials for transformation into products (or perhaps services) for distribution to customers. As given in the value chain definition, those processes are carried out by the various functional areas within the organizations that constitute the supply chain. When considered as a set of processes rather than a succession of companies, the supply chain becomes a little more difficult to identify – let alone manage.
The figures show the flow chart of the supply chain management system or process per value chain definition.
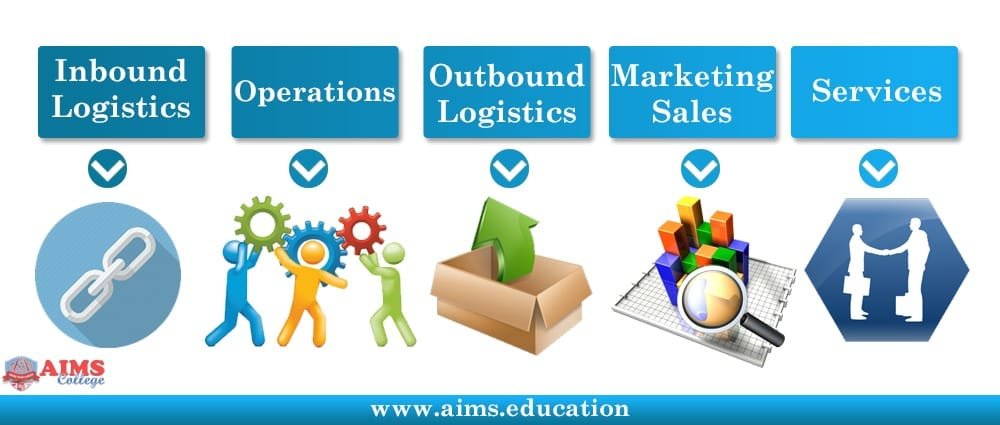
Porter’s Value Chain
1. What is Porter’s Value Chain?
Micheal Porter’s Value Chain focuses on systems and how inputs are changed into outputs. Using this viewpoint, Porter described a chain of activities that are common to all businesses, and he divided them into two types of activities:
- Primary activities.
- Support activities.
2. Primary Activities in Porters Value Chain
They are related to the physical creation, sale, maintenance, and support of a product or service. The primary activities of Porter consist of the following:
- Inbound Logistics are the processes related to receiving, storing, and distributing inputs.
- Operations are the activities that change inputs into outputs. Here, operational systems create value.
- Outbound Logistics are the activities that deliver your product or service to your customer.
- Marketing and Sales are the processes you use to persuade clients to purchase from you instead of your competitors.
- Service are the activities related to after-sales service.
3. Support Activities in Porters Value Chain
They support the primary activities. Each support activity in Porter’s value chain play a role in each primary activity. For example, procurement supports operations with certain activities and marketing and sales with other activities. Support Activities are:
- Procurement is what the organization does to obtain the resources it needs to operate. This includes finding vendors and negotiating the best prices.
- Human resource management is how well a company recruits, trains, motivates, and rewards its workers.
- Technological such as blockchain supply chain are development activities related to managing and processing information.
- The infrastructure of the company’s support systems and the functions that allow it to maintain daily operations, such as Accounting, legal, administrative, cost management, and general management.

Value Chain Mapping
1. Difference Between Supply Chains and Value Chains in Business Operations
Although many would assume that a supply chain is, in fact, a VC at least it is if well managed—others may distinguish between the two. It is a string of collaborating players who work together to satisfy market demands for specific products or services. The value chain is made up of “the functions within a company that add value to the goods or services that the organization Bells to customers and for which it receives payment.”
2. Lifecycle of Products
As it is also explained in a value chain definition, they integrate various supply chain activities throughout the product/service life cycle, from determining customer needs through product/service development, production/operations, and distribution. The intent of a value chain is to increase the value of a product or service as it passes through stages of development and distribution before reaching the end user.
3. Misalignment of Value Chain Activities and Supply Chain Support
Not all VC activities are technically part of the supply chain, and those engaged in them may not understand their role in supporting the supply chain. Those activities might include engineering, marketing, finance, accounting, information technology, human resources, and legal. For example, managers from outside the supply chain often don’t understand supply chain management requirements, can’t distinguish it from a supply chain with supply chain operations reference, and consequently do not provide the SCM support required from their areas.
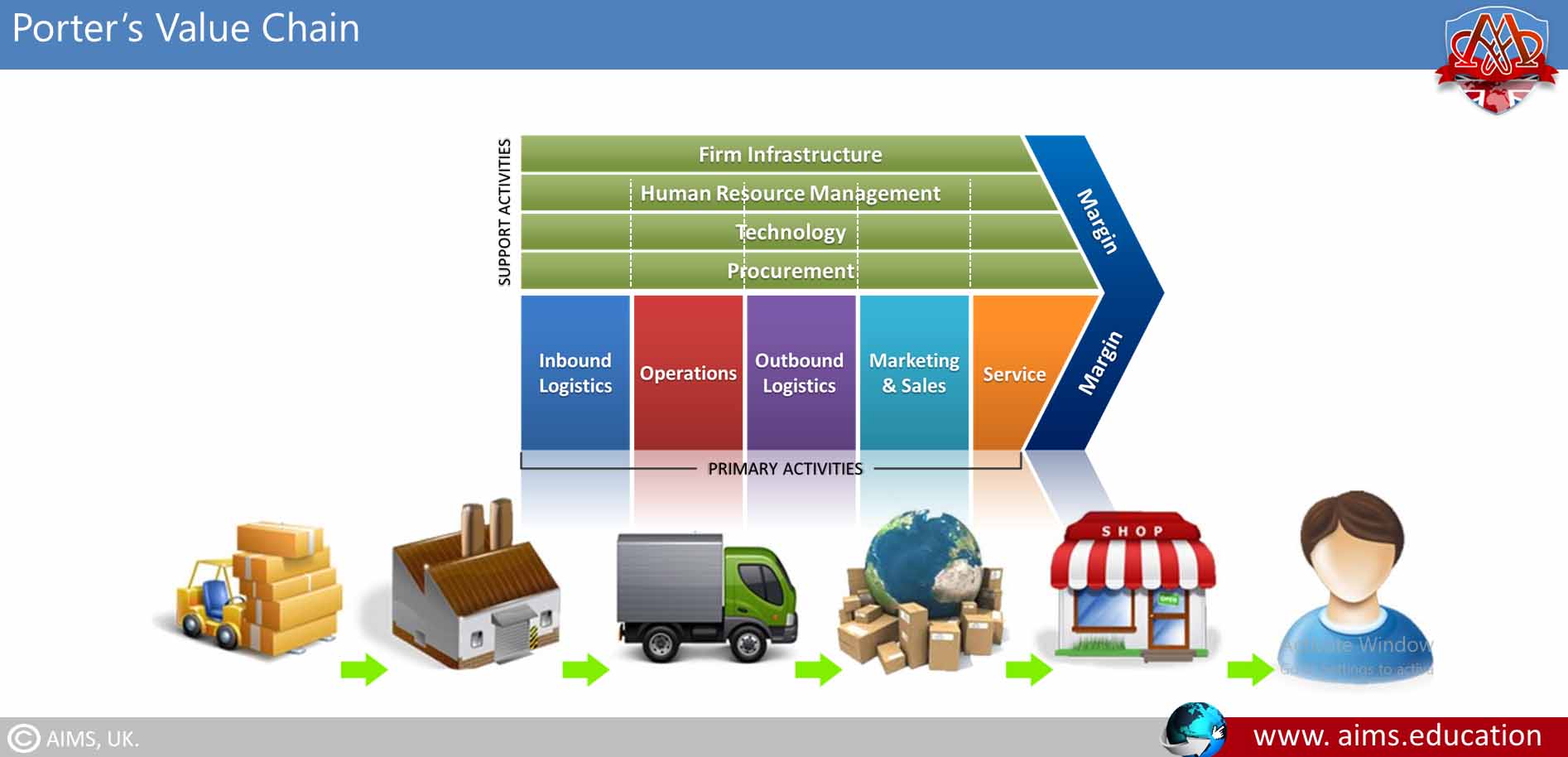
Value Stream: Definition, Components, and Importance
Value Streams and Value Stream Mapping
Two closely related terms are value stream and value stream mapping. A value stream is the processes of creating, producing, and delivering a good or service to the market. Unlike the case of supply chain mapping, the value stream encompasses the raw material supplier, the manufacture and assembly of the goods, and the distribution network. For a service, the value stream consists of suppliers, support personnel and technology, the service “producer,” and the distribution channel. The value stream may be controlled by a single business or a network of several businesses.
Importance of Value Streams Mapping for Process Improvement
A value stream encompasses all the primary actions required to bring a product or service from concept to placing it in the hands of the end user. It also includes timing. Mapping the stream aids in process improvement. A value stream encompasses all the primary actions required to bring a product or service from concept to placing it in the hands of the end user. It also includes timing. Value chain mapping the stream aids in process improvement.
Benefits of Value Chain
- Below are the key benefits of Value Chain:
- Efficiency Improvement,
- Logistics Cost Reduction,
- Customer Satisfaction,
- Strategic Decision Making, and,
- Innovation.
How Do Value Chains Work?
Value chains work by breaking down a business’s operations into relevant activities. These activities are then analyzed to understand how they contribute to the creation of value in a product or service?
- Process begins with raw materials and input acquisition, followed by: Production, marketing, and delivery to the end consumer.
- Each of these stages adds value to the final product or service. Each stage is examined individually.
- This enables businesses to strengthen their competitive position by maximizing value creation and minimizing costs.
1. Support Activities
Support activities, on the other hand, assist the primary activities in improving efficiency and effectiveness. They include:
- Infrastructure (organizational structure, control systems, company culture),
- Human resource management (recruitment, training, development),
- Technology development (technology to support value-creating activities), and
- Procurement (purchasing input for value-creating activities).
2. Examples of Value Chain
- The value chain starts with raw materials like wood, oil, and steel.
- Raw materials are then refined into products like oil and steel.
- These products are then shipped to stores or warehouses where they are sold to customers.
- When a company uses a value chain model, it can visualize how it creates value for its customers.
Value Chain of Toyota
At Toyota, the value chain comprises following several well-coordinated activities:
a. Inbound Logistics
The company’s ‘Just-In-Time’ procurement and inventory management systems ensure that parts arrive when needed.
b. Operations
The company employs a ‘Lean Supply Chain‘, which emphasizes continual improvement.
c. Outbound Logistics
Toyota’s logistics network ensures that vehicles are safely delivered to dealerships once they are produced.
d. Marketing and Sales
Toyota’s marketing strategies focus on reliability, safety, and energy efficiency to attract customers.
e. Service
It includes exceptional customer service, such as warranties, roadside assistance, and scheduled maintenance.
What is Value Chain Analysis?
Value Chain Analysis identifies business activities that can create value and competitive advantage for the organization.
How to conduct a value chain analysis?
Conducting a value chain analysis involves the following steps:
- Identify Activities,
- Analyze Activities,
- Evaluate and Determine Differentiators,
- Identify Links, and,
- Formulate the Strategy.
Growth Opportunities for Enhanced Management
- For beginners, acquiring a certificate in logistics serves as a stepping stone into the career.
- For those desiring convenience and accessibility, an online course in supply chain management and an online diploma in logistics and supply chain are the best choices.
- Aspiring leaders may find an MBA degree in supply chain management and a doctorate in supply chain and logistics gear professionals with strategic and managerial perspectives.