What is Operations and Supply Chain Management?
Supply Chain Operations or Operations and Supply Chain Management (OSCM) refers to the design, operation, and continuous improvement of the supply chain systems to efficiently deliver the organization’s products and services to its’ customers. OSCM is now becoming an essential factor for organizations to stay competitive. The optimization of supply chain management operations has a huge impact on an organization’s success, as good supply chain operations planning eventually positively impacts its growth and credibility.
Managing Variations in Supply Chain Operations
Optimization Supply Chain Operations
In real world scenario, demand for many products changes frequently from period to period, often because of a predictable influence. These influences include seasonal factors that affect products (e.g., lawn mowers and ski jackets), as well as non-seasonal factors (e.g. promotions or product adoption rates) that may cause large, predictable increases or declines in sales.
Predictable variability is a change in demand that can be foretasted. Products that undergo this type of change in demand create numerous problems in the supply chain operations, ranging from high levels of stockouts during peak demand periods to high levels of excess inventory during periods of low demand. These problems increase the costs and decrease the responsiveness of the supply chain. Supply Chain Operations can be improved significantly when strategies are applied to predictably variable products. Faced with predictable variability, a company’s goal is to respond in a manner that balances supply with demand to maximize profitability.
Enhancing Profitability through Effective Supply Chain Operations
The goal of sales planning and the Operations and Supply Chain Management is to appropriately combine two broad options to handle predictable variability:
- Manage supply using capacity, inventory, subcontracting, and backlogs.
- Manage demand using short-term price discounts and promotions.
The use of these tools enables the supply chain to increase profitability, because supply and demand are matched in a more coordinated fashion. One way requires a manufacturer to carry enough manufacturing capacity to meet demand from production in any period. The advantage of this approach is that the manufacturer incurs low inventory costs because no inventory is carried from period to period. The disadvantage, however, is that much of the expensive capacity is unused during most months when demand is lower.
Strategic Inventory Management to Improve Supply Chain Operations
Another approach to meeting demand is to build up inventory during the off-season to keep production stable year-round. The advantage of this approach lies in the fact that Red Tomato can get by with a lower capacity, less expensive factory. High inventory carrying costs, however, make this alternative expensive. A third approach is for the manufacturer to work with its retail partners as per the supply chain strategy to offer a price promotion before the spring months, during periods of low demand.
This promotion shifts some of the spring demand into a slow period, spreading demand more evenly throughout the year and reducing the seasonal surge. Such a demand pattern is less expensive to supply. The manufacturer must decide which alternative maximizes its profitability through its supply chain operations process.
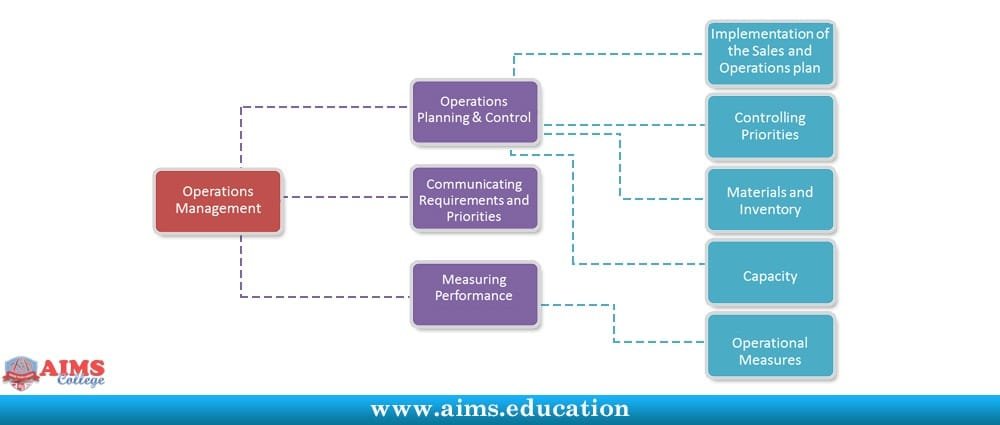
Steps for Supply Chain Operations Planning
The basic steps to control the Operations and Supply Chain Management can be summarized as follows.
- Demand history data are gathered and cleansed. A statistical forecast is run and analyzed for events or outliers that are not expected to repeat in the future.
- The statistical forecast with associated errors is reviewed with the product and brand management, marketing, and sales teams. The teams add information to the demand plan that will improve forecast accuracy.
- The demand plan is finalized with the demand-side teams and passed on to supply.
- The supply team reviews the demand plan and constrains it based on capacity availability.
- Both supply and demand review the constrained plan with the finance team and executive management.
When the executive meeting is held, the result is the communication of a single plan: sales sell to the plan, and supply produces to the plan.
- The output of supply chain operations planning is the production plan, which provides the rate of production at the family level.
- Resource requirements are evaluated with the resource plan.
- The production plan is the input to master scheduling and its output, the master production schedule. The MPS is typically a weekly plan at the item level with an evaluation of capacity through rough-cut capacity planning.
- Then materials requirement planning uses bill of material data, inventory data, and the master production schedule to calculate requirements for materials, resulting in planned production and purchase orders.
- Production activity control receives the output of MRP and detail planning, and final assembly scheduling is done.
The strategic activities of business planning, resource planning, and S&OP are discussed in more detail next.
1. Business Planning for Supply Chain Operations
Making a Business Plan to Improve Supply Chain Operations
The business plan is a thorough and disciplined preview of what the firm hopes to accomplish with its products and services over the long term, with emphasis on the plan year. The business plan is typically stated in dollars and grouped by product family. There may be overly optimistic projections from marketing at some points, but the numbers are there for later review as well as to specify projected revenues, costs, profits, and objectives for the product families all to support the long-range strategy proposed for entering the marketplace. Key inputs to the business plan include the demand plan and its long-term forecasts. Budgets and projected financial statements are key outputs.
A business plan should do the following things:
- Clarify strategy by stating an explicit vision for the business – a reason for being.
- Provide a point of reference for developing the sales and operations plan.
- Describe long-term strategies that will be used to guide shorter-term tactical plans for producing and selling the product.
Strategic Implementation Following the Business Plan
The next steps after the business plan are development of a long-term resource plan and a near-medium-term sales and planning the supply chain operations, based on the longer term views of the business plan. It’s time to start investing in capacity and then using that capacity to make money and provide the lenders and investors with the return on investment (ROI) they anticipated when they signed on as financial partners in the enterprise.
2. Resource Planning for Improved Supply Chain Operations
Long-Term Resource Planning Strategies
Resource planning, sometimes called resource requirements planning, takes the longest view of the system’s capacity, typically going out 15 to 18 months but sometimes requiring much longer planning horizons for capital investments. Resource planning is defined as:
Capacity planning conducted at the business and production plan levels. The process of establishing, measuring, and adjusting limits or levels of long-range capacity. Normally based on the production plan but may be driven by higher-level plans beyond the time horizon for the production plan, e.g., the business plan. It addresses those resources that take long periods of time to acquire.
Relationship Between Resource Availability and Production Planning
The duration of the planning horizon depends on the lead time of the needed resources, which may be a machine to produce the planned product. The total lead time needed would include not only installation time but also the lead time needed to conduct Operations and Supply Chain Management. Equipment or facility construction with long development lead times may be driven primarily by the business plan, while realigning existing facilities and the workforce to change capacity is more likely to be based on the production plan generated during the OSCM process.
Note that capital expenditures in facilities or expensive equipment is an executive-level decision, while the resource planning that is based on the production plan is more likely to be a role of supply chain management decision.
3. Sales and Operations Planning (S&OP)
Sales and operations planning, which we first looked at in Section A regarding using its meetings to synchronize supply and demand, is discussed further in this section, with an emphasis on the overall S&OP functions and process.
Sales and planning of Operations and Supply Chain Management rests on the assumption that firms wishing to compete in the expanding global marketplace can and must break down the silo walls between functions and break through the barriers separating supply chain partners. In fact, S&OP is intended to be a planning and controlling tool not just for manufacturing but also for the entire enterprise. Breaking down those barriers, however, doesn’t always happen quickly and easily.
The most important consideration is the understanding that the plan to generate enough capacity to match supply with aggregate demand must be created, executed, and monitored in collaboration with sales and other functional areas, not in isolation.
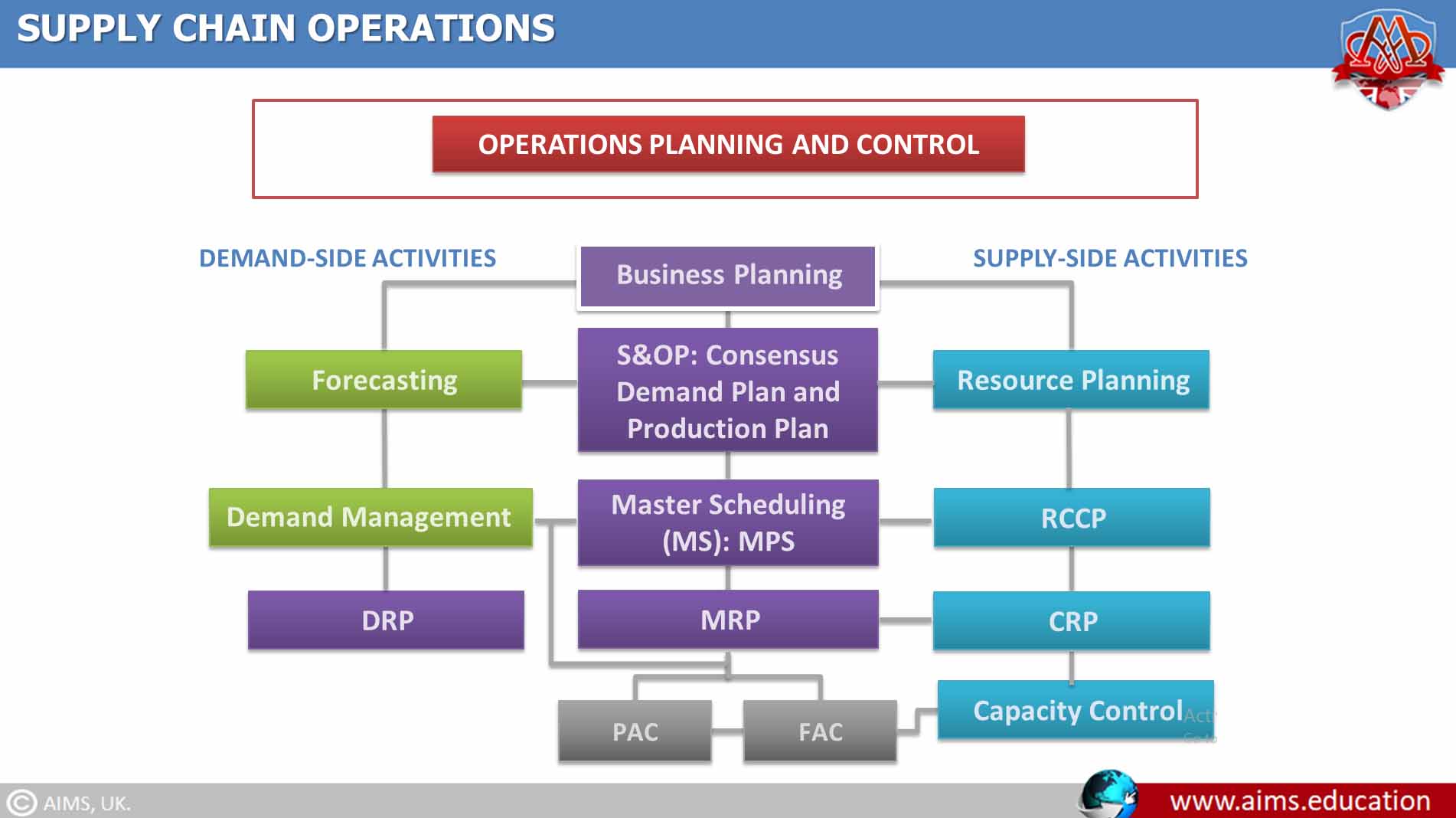
7 Steps in Supply Chain Operations Management
Supply chain operations management requires strategic planning, efficient execution, and continuous monitoring. By following these steps, you can manage operations across the supply chain:
- Step 1: Define Clear Objectives.
- Step 2: Understand the Supply Chain.
- Step 3: Implement an Effective Planning System.
- Step 4: Establish Strong Supplier Relationship Management.
- Step 5: Optimize Inventory Management.
- Step 6: Do a Supply Chain Analysis and Utilize Technology such as blockchain in supply chain.
- Step 7: Continuously Monitor the Supply Chain Operations and Make Improvements.
Challenges in Supply Chain Operations Management
In the realm of operations and supply chain management, several challenges require strategic supply chain management solutions. Some of them are listed below:
- Demand Forecasting.
- Supply Chain Visibility.
- Risk Management in Supply chains.
- Cost Control in logistics and supply chains.
- Supply chains Innovation and sustainability.
- Technological Integration.
- Talent Management for skilled supply chain, transport, logistics, warehouse and procurement manager.
Outsourcing the Supply Chain Operations
Outsourcing supply chain operations can be a strategic move for businesses focusing on their core competencies. The following steps are helpful for organizations considering outsourcing their supply chain operations management:
- Step 1: Identify your business needs and design a supply chain network accordingly.
- Step 2: Search for Potential service providers.
- Step 3: Request a proposal for their operations and supply chain management.
- Step 4: Evaluate different proposals.
- Step 5: Initiate a pilot project.
- Step 6: Review the performance after the pilot project and refine processes accordingly.
Operations and Supply Chain Management Jobs
- An education in supply chain management, such as an MBA in supply chain management and logistics, a diploma in logistics and supply chain management online, or a certificate in supply chain management, can make you a more attractive candidate.
- A doctorate in supply chain management could benefit those aiming for advanced positions.
- Enrolling in the professional institute of supply management provides opportunities for training, networking, and staying updated with the latest industry trends and best practices.